I have had the pleasure of meeting a lot of great hard working Americans over the years. Social media has helped me reach people with whom I probably would not have met otherwise.
US manufacturing is our passion and the same rings true with Co-owner and President of Obsidian Manufacturing Industries Inc., Sue Nordman. Usually I jump on the phone and speak to manufacturing leaders directly, but Sue has a full schedule and was kind enough to do an email Q&A for me.
Please tell our readers a little bit about yourself and then tell us about your role at Obsidian Manufacturing Industries, Inc.
Manufacturing always has been close to my heart with my family having established strong roots in the industry years before me. My father and husband created the foundation I center my leadership style on daily.
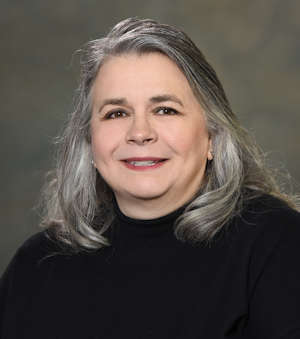
I have only been in a leadership role at Obsidian Mfg since March 2018. Prior to that, I was a part-time employee.
At that time, I was in a position that was very much behind the scenes doing all the accounting and managing the office. My husband was the sole shareholder of the company until I started full time work in 2018.
We both agreed in 2007 when he started the company that my focus would remain on raising on our three children and he would put all his energy into running the company.
By the time our youngest had graduated high school, he was feeling burned out while I was feeling ready to reenter the full-time workforce. So, we formed a plan, and I became the majority shareholder in March 2018.
It has worked out well for both of us because my husband has been able to focus more on what he likes to do, and I get up every morning and head to a job that I love. I like the administrative role and he never really did.
As far as what I do at ObsidianMfg, I touch all aspects of the company daily. I’m a very hands-on leader.
How long has Obsidian been in business?
We were incorporated in 2007 under the name of one of our brands. In 2010 we added two more brands. In 2018 we added yet another brand.
At that point, we really felt like we needed a generic name for the company so our brands could each stand alone. With the original name and then the additions of the other brands, it didn’t seem right to have a brand owning the other brands.
The year 2018 brought some big changes for our company including becoming woman owned. In 2019 we added still another part of our business by purchasing the assets of a grinding shop that had went out of business.
What does Obsidian manufacture?
We manufacture work-holding products and provide repair services under the Magna-Lock USA brand. We also manufacture, certify and repair lifting magnets under the brands of MagnaLift and Power-Grip. And, lastly, we manufacture, rebuild and make spare parts for Arter Precision Grinding Machines. We are the OEM of all 4 brands.
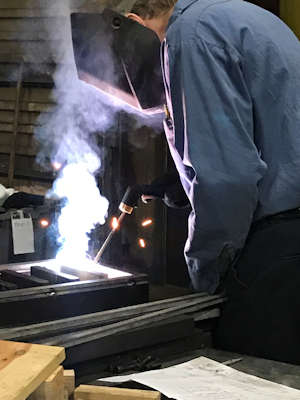
We moved to our current location in May 2019 when we purchased the equipment of the former tenant of the building, Stieg Grinding Corporation. We acquired 3 Mattison Machine Works grinders and one Hanchett rotary grinder and added them to the Mattison grinder we already owned to create a small grind shop. Our grinding services are under the brand ObsidianMfg Grinding Services.
How many employees do you have?
Not enough and currently looking for more! We have been floating somewhere around 10 to 12 employees. At one time we employed nearly 15 which is an accomplishment with only starting out with three in 2007. Our move in 2019 and then the pandemic hitting just a few months later really slowed things down for us.
Why is US manufacturing so important for your company and brands?
Each of our brands have their own stories but they all share the common quality that they have always been manufactured on American soil. None of them throughout all their different ownerships have ever been offshored.
Arter Grinders is our oldest brand and was started in Massachusetts in 1916 by an immigrant from England. Magna-Lock USA and MagnaLift began in the 1940s and 1960s respectively in Michigan with the Hanchett family from Hanchett Manufacturing. Power-Grip was part of the magnetic machine tool line starting in the 1940s with Sundstrand in Michigan.
Collectively, our brands hold a lot of history for our country in the machine tool industry.
On a personal level, I feel it’s important for a country to be able to support it’s people. To do that effectively and efficiently, we need to make things here. I think the economic effects of the pandemic supports this general idea as well.
What kinds of challenges have you faced over the past couple of years?
The pandemic would be number one for me both personally and professionally. I have never done more pivots than in the year 2020. I know most small business owners are in the same boat as myself. That thought is comforting to know. I remind myself often that we are not alone in all of this.
On a more personal level, supporting my family through all the twists and turns of the pandemic has been a lot. I don’t think there is enough talk in our country about how much support the elderly need.
It is most definitely an issue for adult children of elderly parents with complex healthcare needs.
Juggling helping my parents with helping my young adult children get on their feet in their lives, while running a manufacturing business during a pandemic has been a lot. I don’t think enough light gets shined on the sandwich generation—those still parenting while helping their elderly parents.
How can you possibly compete with other countries who are using extremely low paid labor?
We can’t. We can’t make enough profit on the certain models of our products to compete. We can’t make products when we can only break even or lose money on them.
If we have a customer that really needs a model that we can’t make, we have provided quotes for products that we have to outsource. If we do that, we always indicate that the product is not made at our facility. There are only certain vendors we use and always include our industry leading 2-year warranty.
We are very transparent with our customers about what is made in our facility.
Many US manufacturers are having issues with finding skilled workers. Are you have the same issues and if so, how are you addressing them?
Yes, we are having the same issues. We are using every means possible to get people in here and trained. Temp agencies, staffing services, job sites, word of mouth are just a few of the ways we are approaching the labor shortage.
What kind of advice would you give to young men and women who are torn between going to college and picking up a trade?
I have one child currently in college and another that has their bachelor’s and master’s degrees so I’m completely supportive of college. But I also support tech schools and hands on experience. It’s a personal choice for everyone.
As a country, we have talked negatively for so many years about the trades. That it is going to take a big push in the opposite direction to make some headway. I don’t think we will see the effects of things starting to change for at least another 10 years. It’s going to take that long for significant steps in the right direction to happen and then many more years to make a big difference.
What would you like to see in the future for US manufacturing?
A more positive perspective from our country as a whole. More support from the public and the politicians. There is nothing wrong with a person’s hands getting dirty from earning a living and our country needs to support that idea. We got away from it and it’s going to be very difficult to get back to where we need to be.
###
Obsidian Manufacturing works with a variety of industries from aerospace to construction to woodworking and more.
If you want to learn more about Obsidian Manufacturing Industries Inc. and the manufacturing services they provide or you are in the Rockford, Illinois area and looking for employment, then please visit their website at https://www.obsidianmfg.com/